Written by Aleksandar Pavic.
Since Engineered Vibration Solutions Ltd launched our CALMFLOOR product at the beginning of 2021, I often get asked: how can a practicing engineer engage with it? How can they check if their design can benefit from the world-first commercial active mass damper (AMD), an autonomous mechatronics device, for controlling resonant vibrations in low-frequency building floors?
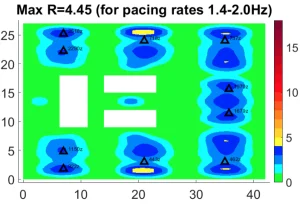
CALMFLOOR actively generates unprecedented amounts of damping force in a low-frequency floor vibrating in resonance. Therefore, the best way to check what it can do is to simply assume equally unprecedented levels of viscous damping ratio in all low-frequency modes of vibration which need controlling, having natural frequency typically below 12Hz. So, if you are using back-of-the-envelope calculations, a spreadsheet, or an advanced structural analysis package with a footfall vibration analysis option in it, simply assume a 10% (ten percent!) damping ratio, rather than the usual 1-2.5%, in all relevant modes of vibration. Then do the floor footfall vibration calculation or computer analysis as usual. This will give an indicative level of the vibration reduction that typically can be achieved with our CALMFLOOR dampers.
Typical Vibration Response Analysis
The first figure shows a contour plot of response factors for a typical long-span low-frequency steel-concrete composite floor spaning 14m. A damping ratio of 2% was assumed for all modes of vibration, which is reasonable for long-span open-plan composite floors supporting modern paperless offices. White areas indicate lift and staircase shafts, suggesting a fairly detailed finite element modelling of this floor. The floor also has 14m long secondary beams which feature in so many modern office buildings. The total floor area, consisting of 3 by 3, 9m wide, and 14m long floor panels, was just over 1000m2.
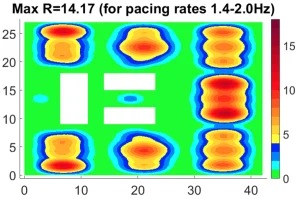
Above Image: Contour plot of response factors for a typical long-span low-frequency steel-concrete composite floor spaning 14m
So, it is a decent size floor plate with a standard 130mm deep lightweight concrete deck, steel beams, and columns. It has an admirably low mass of 231kg/m2 and an equally reasonable embodied energy of 201kgCO2e. This floor structure satisfied the strength, deflection, fire resistance, thermal comfort, and sound insulation design requirements with the minimum structural mass. However, the contour plot shows that about 25% of the floor area has a vibration response factor R>4 for a single person walking with the maximum R>14.The floor comprehensively failed the vibration serviceability check for an office following the key international standard ISO10137.
Structural Modifications
The structural modifications needed to bring this floor back to vibration serviceability with R<4 over more than 99% of the floor area required that the mass of the floor almost doubled to 452kg/m2 with the total floor depth 260mm greater and embodied carbon 30% higher just for the floor structure. The obvious additional consequences on the whole life cycle cost of the building, including the increases of the cost of foundations, construction, and decommissioning were not considered. Needless to say, with so much greater floor depth, a typical multi-storey commercial building featuring floors like this and with a normally limited height in an urban environment, would lose one entire usable floor level every dozen or so floors. Obviously, the cost of the omnipresent structural modifications to meet the R<4 floor vibration serviceability requirement is colossal and very much unacceptable. What then?
Results of Assuming 10% Damping
Well, this is the moment when the above-given advice on the 10% damping ratio in all relevant modes should be followed. The second figure shows the response factors for the floor before any structural modifications, assuming 10% damping ratio. Top-quality office floor vibration performance (R<4) has been achieved on almost all of the floor area and – remarkably – without any structural modifications needed.
But, how reliable is such a simple floor vibration serviceability analysis to incorporate the effects of floor AMDs?
Image to the right: Contour plot of the response factors for the floor before any structural modifications, assuming 10% damping ratio
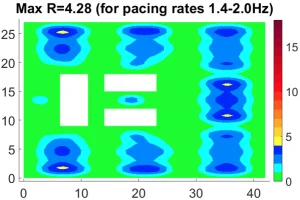
A simple visual inspection of the last two contour plots suggests that the results of this detailed analysis match very well, indeed, the ‘10% damping ratio’ results. It should be stressed here that the cost of 10 CALMFLOOR units is at least an order of magnitude lower than the direct and indirect costs of the structural modifications. Or, to put it more positively for the architects and developers – the CALMFLOOR technology would not only enable the significant 14m long-span of this floor to be maintained (with all its commercial and well-being benefits for its human occupants) without any structural modification but would also enable additional floor levels in case this floor features in a multi-storey building with dozen or so floors and with the customary urban height restrictions.
This confirms that the 10% damping ratio is a very reasonable rule of thumb when initially engaging with the CALMFLOOR technology. If you get satisfactory performance, get in touch with me to discuss the CALMFLOOR solution for your floor vibration problem.