Written by Aleksandar Pavic.
Over the last 10 years, I published with my researchers and collaborators dozens of technical and scientific papers dealing with vibration serviceability of civil engineering structures. Chiefly under human-induced dynamic loading, such as walking on floors. The opening sentence of such papers typically reads:
“With the advent of stronger and lighter construction materials and advancements in construction technology, vibration serviceability has become a governing design criterion. This creates lightweight and slender civil engineering structures occupied and dynamically excited by humans.”
So, in the case of open plan and long-span floors, it’s not the strength (i.e. the threat of structural failure) but vibration (i.e. the threat of excessive dynamic motion) which dictates the size and shape of such structures. Laypeople are often perplexed that anything other than serious structural failure and threat to life can dictate the design. The use of literally millions of tonnes of construction materials and associated embodied carbon seem to be overlooked. Very often, in situations like this, I get asked a simple question: how much more material and embodied carbon is then needed just to have satisfactory floor vibrations?
Doubling Floor Weight to Control Only Tiny Floor Vibrations
The case study of a long span floor
The contour plot in Figure 1 shows the plot of response factors due to walking over a 42m long and 27m wide (1,134m2) floor plate consisting of nine floor panels. Each of these spanning 14m and being 9m wide. So, it’s a typical long-span composite steel-concrete floor which can be found in many modern commercial buildings in the UK and internationally. The floor, featuring the usual 14m long secondary beams to minimise the number of beam-to-beam connections, was optimised to have minimum weight and structural depth. This still satisfied all design criteria (strength, deflection, fire resistance, thermal comfort and sound insulation) apart from vertical floor vibrations. Maximum vertical vibrations allowed were set to response factor R<4, as appropriate for an office in accordance with the relevant, respected and widely used international standard ISO 10137. In the UK that would be a ‘quiet office’. The floor’s 130mm deep lightweight concrete deck, beams, and columns had an admirably low mass of 231kg/m2 and equally reasonable embodied energy of 201kgCO2e. However, as Figure 1 shows, 25% of the floor area (warm coloured) had R>4 with the maximum R>14, and the floor clearly failed the vibration serviceability check.
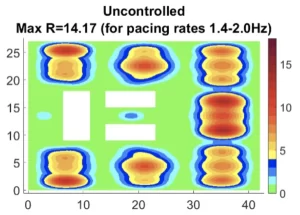
The outcome
The usual structural modifications followed which, after many iterations, yielded again a floor structure with minimum weight and depth. However with R<4 over 99% of its area, the mass of that structurally modified floor almost doubled to 452kg/m2 with the total floor depth being 260mm greater. The embodied carbon 30% greater just for the floor structure. The obvious consequences on the whole life cycle cost of the building need to be considered. These increase when considering the cost of foundations, construction, and decommissioning, they were not considered. The greater floor depth on a typical multi-storey commercial building featuring floors like this and with a normally limited height in an urban environment, would lose one entire usable floor level every 12 floors. So, the cost of structural modifications to meet the R<4 floor vibration serviceability requirements is obviously colossal and very much unacceptable. What then?
Image on the right : Figure 1 Uncontrolled floor designed for minimum weight satisfying all design criteria apart from vibration serviceability
4‹R‹8 Can and Did Create Excessively Lively Floors
Alternatives to control vibration
One often seen in practice approach is to relax the floor vibration serviceability requirement and go for R<6 or R<8. However, over the years I dealt with quite a few problematic floors with unhappy tenants and demonstrably with 4<R<8. Others have reported issues with such floors as well. I have to say here that, scientifically, there is not much proper science and peer-reviewed evidence that would justify R>4 for offices. Hence, R<8 for offices seems to be driven by the obviously very high environmental and financial cost of meeting R<4. However, this fact of life is somewhat muted with 4<R<8 becoming a de-facto norm with an expectation that the floor will behave well. Nevertheless, 4<R<8 could attract a considerable number of complaints under certain conditions. Unfortunately, those conditions are currently not clear and require further scientific research.
Contact us for more on Active Mass Dampers
Please get in touch if you are interested in such research. I actually wrote a conference paper that tried to present some available evidence about vibration problems with ‘code compliant’ building floors. The history of the R<8 criterion, and presented it at the SECED 2019 conference. Check paper 25.7 in Session 25 – Vibration Serviceability. Having all this in mind, what is then the way forward when:
a) meeting R<4 criterion is prohibitively expensive, and
b) not meeting R<4 can seemingly easily create an unduly lively floor attracting complaints and which is difficult to let and fix?
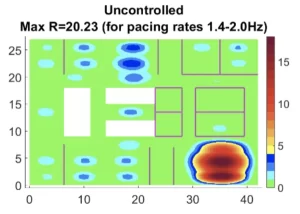
Other factors that effect vibration
Figure 2 shows the contour plot of R-factors for the same unmodified lightweight floor structure featuring full-height non-structural partitions (outlined in pink). These partitions are typically present in every office, but their stiffness is normally neglected. This despite the fact that there is a growing body of published peer-reviewed evidence that non-structural partitions can completely change the dynamics of the floor rendering bare floor calculations potentially useless. After all, this is very much the experience of anybody who witnessed a normally lively bare composite floor transforming into a well-behaving floor in the partitioned areas. Following recommendations from some recent peer-reviewed publications, the vertical stiffness of the outlined partitions was modelled using simple vertical springs. It can be seen that the partitions very much suppressed vibrations in the partitioned areas, as expected. But, the partitions also amplified vibrations in the not-partitioned open-plan part of the floor, boosting the maximum R-factor to over 20.
Although the experience is also that not-partitioned areas of the floor are known to be lively, such a significant amplification of vibration is a somewhat surprising result.
When comparing contour plots in Figures 1 and 2, it can be seen that the response factors in the unpartitioned area of the floor (bottom right corner) are almost 50% greater than when calculated neglecting the presence of the partitions. This means that the common belief that neglecting partitions is a ‘safe’ assumption may well not be correct. This may concern many colleagues as it definitely concerned me.
Image on the left: Figure 2 The original lightweight composite floor not satisfying vibration serviceability, but with floor partitions modelled
Solution For 21st Century: Sophisticated Vibration Analysis Coupled With CALMFLOOR®
The last contour plot in Figure 3 shows R-factors for the structurally unmodified, original lightweight floor, featuring partitions and effects of only two CALMFLOOR active mass dampers in the problematic unpartitioned area. The floor plate has satisfactory R<4 performance over practically the whole of its area without any structural modifications or the need to relax the vibration criterion potentially creating an unduly lively floor to save on materials. The very small carbon footprint of the two CALMFLOOR units (relative to the mentioned structural modification) and their competitive costs mean that both environmental and financial costs of the CALMFLOOR solution are many, many times lower than those of the structural modification to achieve the coveted R<4.
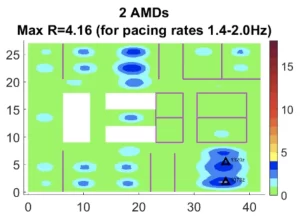
The usual argument against an approach that involves explicit modelling of the partitions is that it is normally not clear where the partitions are going to be until the tenant moves in. The counter-argument is that sooner or later the floor partitions will be erected and then it will be clear where the unpartitioned areas are. The 70kg CALMFLOOR units can then be installed there causing no disruption. That can be done very easily and with the full cooperation of the tenant after they move in. This is probably the key transformative feature of CALMFLOOR: it is new off-the-shelf technology that is dead easy to install. This is in stark contracts with other post-occupancy solutions to control floor vibrations such as:
the structural modification, or
installation of at least an order of magnitude heavier tuned mass dampers (TMDs) which are likely to perform less well and cost very much the same or more than the CALMFLOOR active mass dampers.
So, combining the sophisticated modelling of partitions with CALMFLOOR units in the remaining unpartitioned floor areas is a new design approach that enables keeping long and very lightweight spans which also have excellent vibration performance impossible to achieve today by any other means.
Philosophically, structural engineers designing buildings tended to deal with many structural design uncertainties by throwing relatively cheap construction materials at them, as no better approach existed. The climate emergency means that such a practice has to stop immediately. In the case of uncertainties related to floor vibration serviceability (location of partitions, corridors, number and activity of office occupants, future tenant’s vibration serviceability needs, etc.) CALMFLOOR is really a game-changer: it can be deployed flexibly and easily only at floor vibration ‘hotspots’ after the handover of the building and the tenant and their needs are known. Compare that with the wasteful structural modifications which need to be done everywhere before the unknown tenant comes in.
Image on the right: Figure 3 The original long-span composite floor featuring full-height partitions and two CALMFLOOR units reducing the maximum R-factor from highly problematic 20.2 to satisfactory 4.2 in the problematic unpartitioned area of the floor