The real cost of controlling floor vibration: CALMFLOOR active floor vibration control -v- the alternative solutions
If you have a vibrating floor problem in your building, the traditional costs to remedy it can be as catastrophic as the issue itself and extend far beyond materials and labour. In new-build properties that call for mitigation against potential vibration issues, balancing budgetary challenges with leaner design ambitions and sustainability constraints too often mask the true cost that, with a little innovation, could be cut dramatically.
We’ve explored the often underestimated, but very real cost of controlling floor vibration that makes the case for CALMFLOOR active vibration control so compelling.
Traditional approaches to reduce floor vibration
So, you’ve identified a floor vibration problem in your existing building – these are the choices you’re faced with:
1. You destroy the floor and/or the building.
2. You intervene structurally and build a line of columns.
3. You fit tuned mass dampers (TMDs).
4. You pour more concrete and/or add more steel.
Alternatively, you could fit CALMFLOOR AMDs and reduce your floor vibration by up to 90% in hours – at a cost you might never have thought possible. Here’s why:
The time cost
We don’t account enough for the months of planning some of these structural modifications to a building will cost the project. While big project groups collaborate and deliberate, the building is non-operational, non-compliant and losing ‘opportunity cost’ and valuable revenues.
CALMFLOOR AMDs are the fast, fit-and-forget solution with a unique, try-before-you-buy simulation service that will give you the evidence and confidence you need to make the switch fast. Units are installed in just hours, eliminating the entire planning time phase altogether.
The materials cost
The costs of moving concrete and steel are exorbitant and well documented. But this is where we need to get technical. CALMFLOOR uses damping ratio zeta to replace modal mass in the resonant formulas: Acceleration=Force amplitude/(2*zeta*modal mass). CALMFLOOR generates 4-8 times greater modal damping than the uncontrolled floor – that’s equivalent to having 4-8 times greater modal mass. In practical terms, this may yield to at least halving the physical mass made of a combination of steel and concrete spread over the surface of the floor. This is impossible to achieve by using mass in practice but, with CALMFLOOR, it is.
CALMFLOOR AMDs are truly the lowest cost and most versatile vibration control solution. Check out our pictures of the team moving our 67kg CALMFLOOR units around like suitcases as you consider the cost of adding steel or concrete to solve your building vibration problem.
The carbon cost
The challenge faced by building owners, operators and engineers striving to meet increasingly stringent sustainability and Net Zero targets has never been more intense. It’s reassuring to know that CALMFLOOR offers considerable savings in terms of carbon impact – here’s how:
We all want to build lighter with reduced floor thickness to make savings on embodied carbon. In a new-build lab campus project, we showed how CALMFLOOR AMDs would enable our client to reduce floor thickness by 40% (from 375mm to 225mm), reducing floor vibration by 75% (from R-Factor 7.3 to 1.9). The approximate savings on embodied carbon were 150kgCO2e/m2 per floor, per level. This is substantial reduction in embodied carbon, floor thickness and vibration.
By using a single CALMFLOOR unit in a 50m² space, further embodied carbon savings can be achieved. With CALMFLOOR you can expect less than 10 kgCO2e/m² in embodied carbon emissions on a thinner floor – without relying on steel or carbon.
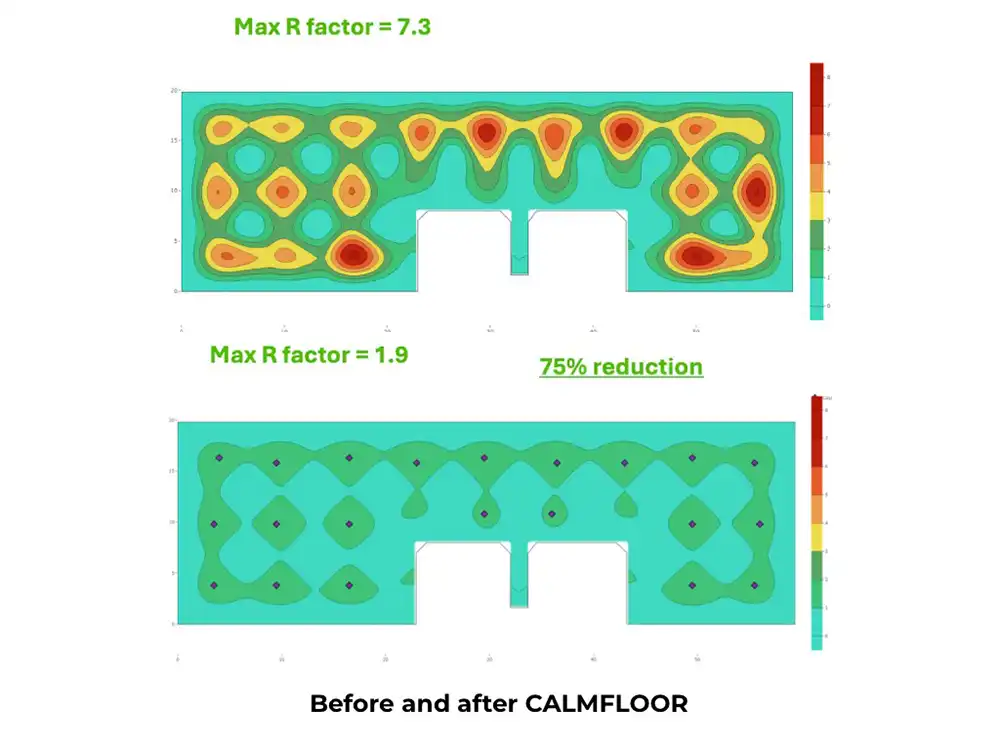
Operational carbon savings are also on the table. While conventional solutions that call for steel and concrete to support the entire floor area and meet vibration performance standards, CALMFLOOR enables you to target the precise areas you want to control. There are further advantages here for partitioned spaces with vibrations: CALMFLOOR’s flexibility means that if a layout change is needed, partitions can be removed or relocated with vibration still controlled by portable, versatile CALMFLOOR AMDs. Read on for more on what this means for building value cost.
The building value cost
Indeed, this versatility is crucial: CALMFLOOR AMDs control vibrations only in the pre-defined hotspot areas that need it. No additional columns or span-shortening are required meaning the current long- and open-span structural transparency and flexibility is completely preserved. Consider the aforementioned partitions that can be moved to suit changes of tenant or use – no other vibration control method can accommodate this without structural intervention.
Remember, the value of your building asset is reduced if its flexibility is compromised. CALMFLOOR is the most versatile floor vibration control solution – it offers flexibility and value straight out of the box.
The insurance cost
It’s also worth factoring in CALMFLOOR’s potential for lower insurance premiums as the risk of unsatisfactory and non-compliant floor vibration levels is so dramatically reduced. CALMFLOOR AMDs are deployed only where and when needed. In comparison, traditional methods are prone to unsatisfactory performance due to errors in design and unpredictable non-structural partitions that impact the dynamic performance of the floor.
CALMFLOOR is the only out-of-the-box solution for low-vibration, high-performance environments
It’s clear that CALMFLOOR makes sound financial sense and, as our clients adopt this revolutionary AMD technology across spaces in the UK, US and Europe, it has fast become the most cost-effective floor vibration solution in the world.
Talk to the team today to discover the savings you can make with CALMFLOOR.
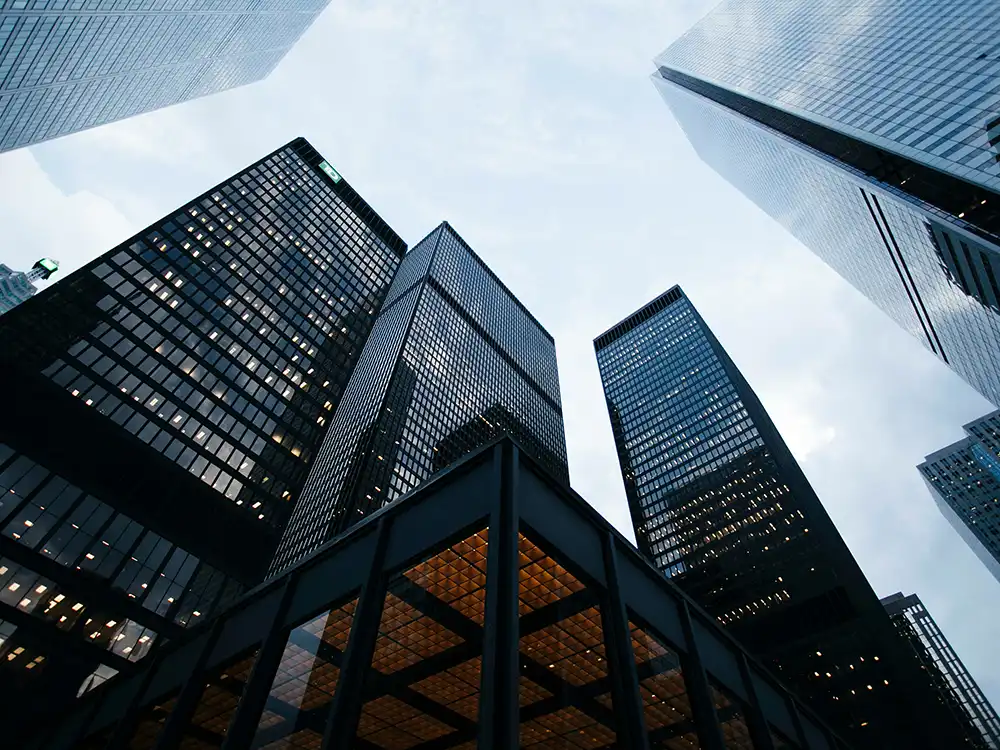